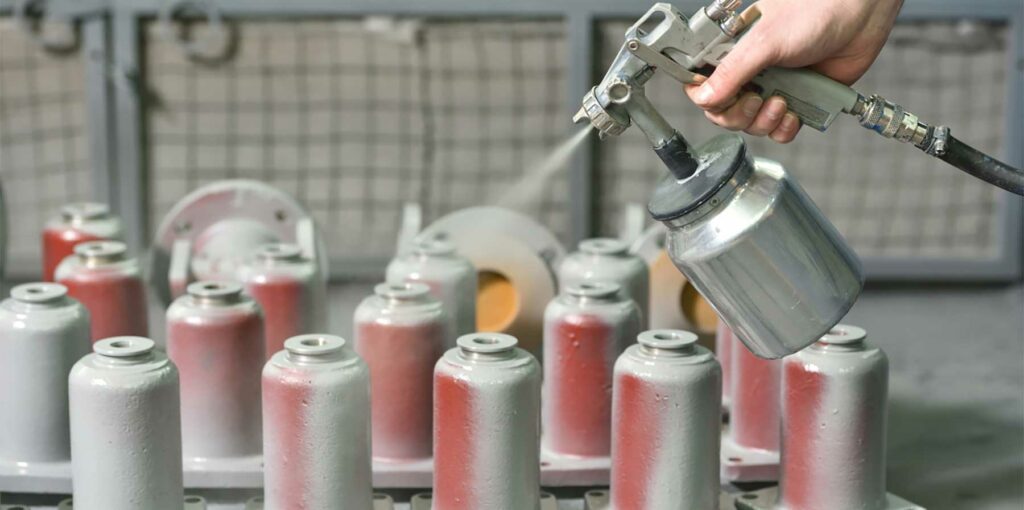
Surface preparation refers to the various methods used to prepare the surface of a material prior to the use of a coating or adhesive. Highly engineered coatings and adhesives are designed to maintain their adhesion in a variety of harsh and unrelenting environments for many years. Coatings for marine applications are designed to protect against corrosion from seawater, and polymer degradation from sunlight. Adhesives used in power generation and electric motors are designed to perform at high temperatures under significant mechanical stresses. Regardless of the application, the success of any coating or adhesive is critically dependent on proper surface preparation.
WHY
Proper surface preparation allows for complete bonding of a product’s chemistry to the substrate.
WHAT
“Good” surface preparation results in a surface free of rust, grease, dust, oil, and other contaminants, and can be achieved chemically and/or mechanically.
Fortunately, various industry groups such as NACE, SSPC (the two are now combined as AMPP), and ISO have defined and specified different levels of surface preparation for various surfaces. These standards provide guidelines to maximize the surface life of a coating or adhesive and allow manufacturers and users to define the desired finished conditions within existing frameworks. Surface preparation standards have also been crucial in developing performance standards for coatings and adhesives.
HOW
Surface Assessment
Prior to surface preparation, it is important to assess the condition of the surface and understand the final surface finish requirements. For example, a rusted steel surface that needs to be returned to a fine surface finish will require rigorous processing as compared to one that requires a less stringent, hand-tool-cleaned finish. A thorough evaluation of the surface with the end goal in mind will dictate the processes required to achieve the optimal end result.
Removal of Existing Coatings
First, any existing coatings should be removed to facilitate good adhesion to the surface. Many paint systems, such as epoxies and urethanes, should be fully removed as adhesion to those coating surfaces is very difficult, especially after years of exposure to the elements.
Removal of Contaminants
All oils, greases, rust, scale, and loose particulate matter must be removed. It should be noted that some surface preparation standards allow for a percentage of scale to remain. It is therefore important for the user to be cognizant of the standard to be utilized.
Surface Profiling
Once contaminants are removed, the surface needs to be profiled to the required topography. This entails physically changing the surface topography to maximize surface area and to remove any persistent loose material not removed in the second step. Profiling can be accomplished through mechanical or chemical processes. In some cases, using a solvent with a lint-free cloth is sufficient to prepare the surface for cleaning.
Chemical cleaning/profiling
This step is typically performed in manufacturing settings due to the equipment and infrastructure required. Basic cleaning processes will remove stubborn oils, greases, and other petroleum-based materials, while acid etching of metals produces a very consistent and clean surface. Once completed, both steps require a thorough rinse and drying prior to coating application.
Mechanical cleaning/profiling
This can be as simple as abrading the surface with a wire brush or sandpaper. More thorough processes include the use of power tools and media blasting to abrade and clean the surface. The most common blasting media is aluminum oxide grit (sandblasting). Softer media such as ground walnut shell is used for soft surfaces such as copper. ‘Clean’ blasting media entails the use of frozen carbon dioxide pellets (dry ice) and is used in applications where media residue is a concern, such as MRO and field environments. The advantage of dry ice blasting is that once it is used, the dry ice immediately sublimes leaving no left-over blast media.
Surface Drying
Coatings and Adhesives perform at their best when applied to a clean, dry surface. Trapped moisture can cause finish imperfections, extended dry time, and lead to premature corrosion and adhesive failure. Humidity should also be considered prior to application as it can adversely affect the dry time and service life of an adhesive or coating once applied.
Every application will have unique requirements based on the substrates involved and the type of chemistry employed. Operators and engineers charged with applying a coating or adhesive should work with the manufacturer to understand the recommended surface preparation.
As a manufacturer of engineered coatings and adhesives, the Astro Chemical technical staff is well-versed in the many aspects of surface preparation. Please reach out to discuss your application. We are happy to help you design a plan for optimal surface preparation.