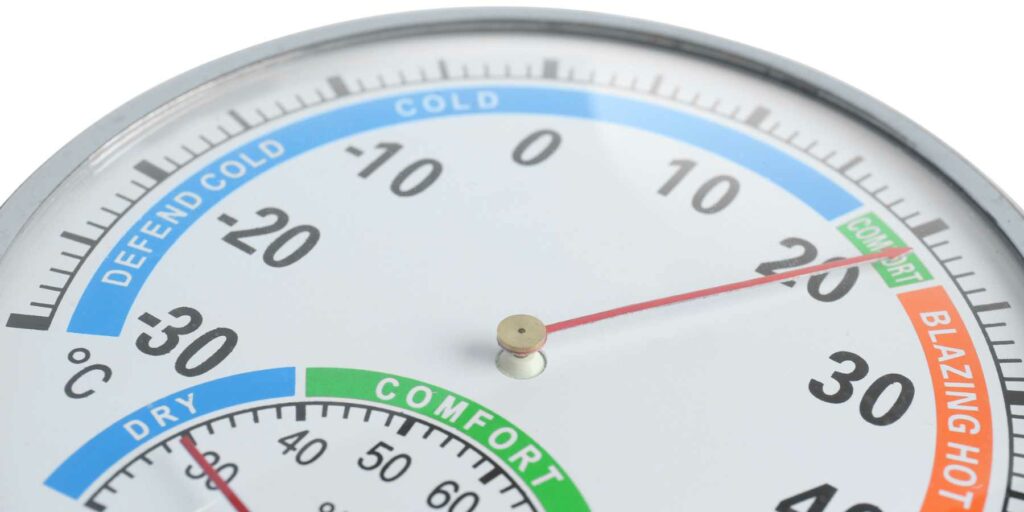
When it comes to using room temperature curing products, it is important to consider the effects of ambient temperature and humidity on the curing process. While we typically recommend applying and curing our products under ideal conditions — 70-75°F (21-24°C), with humidity below 40% in a well-ventilated environment — we understand that this is not always possible, especially in field-service applications.
In these suboptimal scenarios, high or low temperatures and excessive humidity can have adverse effects on cure time, surface appearance, and final cure properties. Therefore, it is crucial for users to be aware of ambient conditions and how they may influence the handling and cure rates of coatings, adhesives, saturants and encapsulants.
Temperature
Temperature plays a significant role in the cure rate of epoxy and polyester resin systems. Cooler temperatures below 65°F (18°C) will slow down the cure rate, unless the product is specifically formulated to cure in colder conditions. On the other hand, higher temperatures above 80°F (27°C) will accelerate the cure rate. Two key concerns regarding temperature are the effect on the pot life (working life) of a mixed resin system and the cure speed of the product once applied.
Epoxy and polyester resin systems exhibit predictable cure rates based on the curatives (hardeners) used. A rule of thumb states that the rate of reaction will double for every 10°C (18°F) increase in ambient temperature, and will halve for every 10°C (18°F) decrease in ambient temperature. In cooler conditions, the pot life of a mixed resin system will increase due to the slower cure rate, allowing for longer working times. Unfortunately, the same reduced cure rate means the product may take significantly longer to fully cure.
The amount of product catalyzed also plays a significant role in rate of cure. For example, when an encapsulating system is catalyzed, its greater mass will generate significant heat due to the exothermic cure reaction. This self-generated heat, due to the greater catalyzed mass, will help to mitigate the impact of suboptimal temperatures. Conversely, in the case of coatings, adhesives, and saturants, which are applied in thinner, small mass films, the small amount of heat generated from the cure reaction dissipates quickly, resulting in a significant drop in the cure rate. In this scenario, the benefit of a longer working life is outweighed by the slower cure rate and extended time required for these materials to fully cure.
Relative Humidity (%)
Relative humidity refers to the amount of water vapor present in the air relative to its maximum capacity at a given temperature. Humidity can impede the drying of solvent and water-based coatings, as high humidity inhibits solvent and water evaporation. When applying solvent and water-based coatings and adhesives on humid days, they may dry significantly slower due to the concentration of water vapor in the air. In such cases, blowing air across the surface of coated parts can reduce vapor pressure and accelerate evaporation. Applying heat can also help to accelerate cure however, it should only be done after consulting with an Astro Chemical technical representative. Excessive use of heat may cause the surface of a coating to cure prematurely, potentially trapping solvent or water vapor within the resin film.
Under humid conditions, certain epoxy chemistries may experience increased cure time and/or exhibit a slick or “greasy” surface feel. This occurs in epoxy resin systems that utilize aliphatic amine curing agents which react with carbon dioxide in the air, creating a hazy appearance on the surface. This is a phenomenon known as “blushing” in the coatings industry. Blushing is more pronounced in humid conditions, although it can occur in any humidity. While blushing will disappear over time, applying mild heat and/or using forced air across the surface can expedite its resolution. It is important to note that blushing is a surface phenomenon and does not affect the curing of the coating or adhesive film.
High humidity environments can also significantly impede the curing process even when blushing is not observed. Internal studies have shown that relative humidity above 60% can increase cure time by tenfold (days instead of hours), and even a 0.1% increase in moisture content within the mixed resin led to a 30% increase in cure time, within a certain group of epoxy chemistries. However, once the moisture is removed, the reaction will resume and the chemistry will fully cure. In extreme cases, the application of heat may be necessary to restore the cure rate to normal levels.
Dew Point
The dew point represents the temperature at which the air is saturated with water vapor. Fog and clouds are examples of water-saturated air. It is crucial to avoid applying a coating or adhesive when the dew point is within 10°C (18°F) of the ambient temperature. When the ambient temperature is close to or above the dew point, condensation may form on the substrate to be coated or adhered. It is essential to avoid applying catalyzed product to surfaces exhibiting condensation. In a factory setting, this may require air conditioning to remove moisture from the air, while field applications may require mildly heating the air to dry parts before coating or adhering. In extreme cases, it may be necessary to wait until the ambient conditions improve.
Conclusion
Operators and engineers should always consider the ambient conditions before applying a coating, adhesive, saturant, or encapsulant resin system. If the ambient conditions are questionable or if any of the above phenomena are observed, do not hesitate to contact Astro Chemical for a technical consultation. We are always here to help you achieve optimal results in your application process.